1.Preamble
One-piece door rings are very popular in mainstream car companies because of their economy and safety. Because of the different force and structural requirements of different parts, different thicknesses need to be realized in different parts, called reinforcement sheets or patch plates, so they need to be in After tailor welding of the door knocker and before thermoforming, pre-spot welding is required with the patch plate (mainly used for the AB pillar reinforcement plate).
Process analysis:
2.The base material of one-piece door ring before thermoforming is mostly boron steel, the yield strength is 280-400Mpa, and the welding performance is good. Considering that the shape of the door ring material is larger than that after forming, and there are many solder joints on the patch board, it is often used Automatic feeding method, automatic spot welding after assembly.
3.Case:
The door knocker of an automobile factory M project, material 22MnB5, thickness 1.6MM, two patch boards, a total of 78 solder joints, found us through a friend's introduction, we use robot automatic loading, robot welding torch spot welding, automatic unloading.
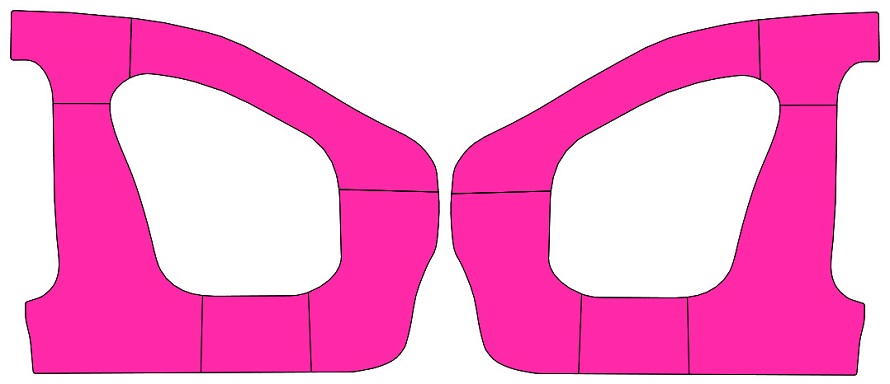
3.1 Scheme layout:
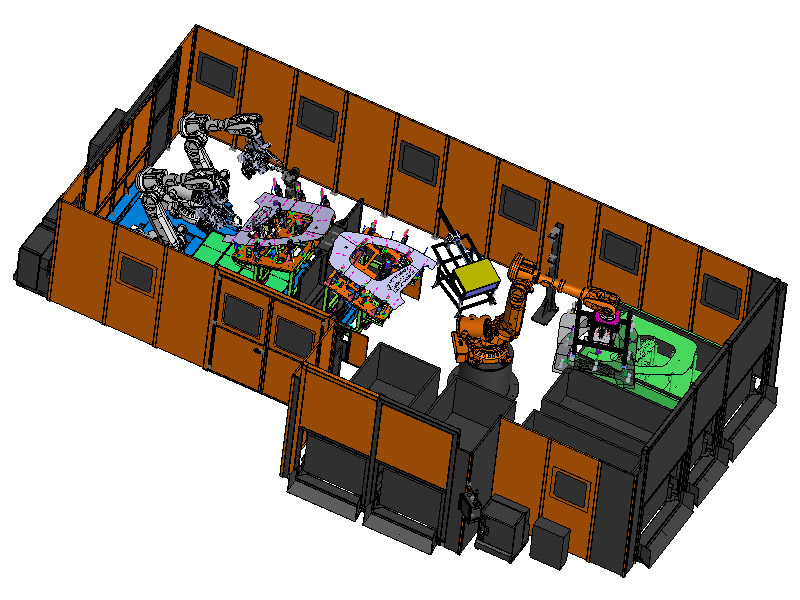
3.2 Project Introduction
The incoming material is in the form of a material truck, which basically constrains the shape of the workpiece, and then grabs it through the robot suction cup and calibrates the position, and transports it to the turntable tooling, and then after clamping, it is marked by two Anjia welding torches (due to the large number of solder joints, double guns are used for spotting) ), after spot welding, the robot unloads the material to the feeding truck.
a.Grabbing station: the workpiece is sucked up from the material truck by the vacuum suction cup, and then transferred to the tooling after reaching the turntable;
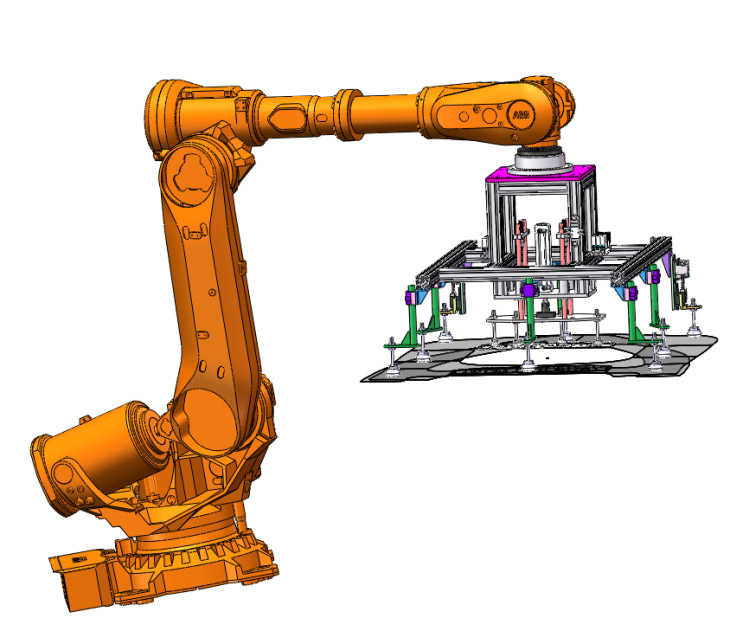
b. Double welding gun station: two robot welding guns are simulated and welded synchronously according to the best path;
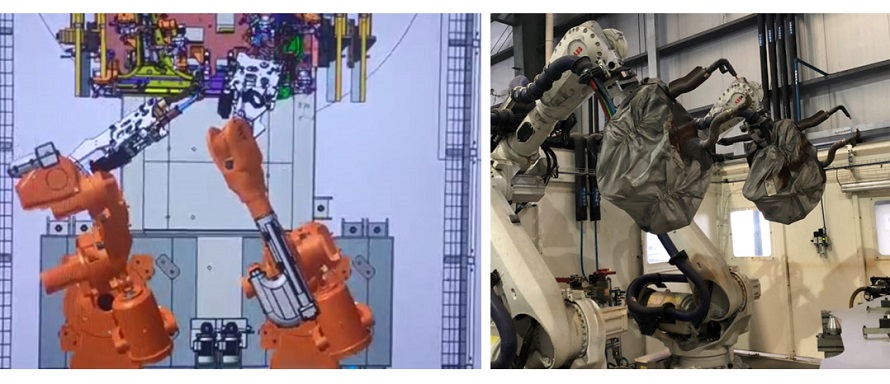
b. Rotary tooling: Due to the large shape of the workpiece, the inclined tooling is used to reduce the footprint and shorten the reachable stroke of the robot;
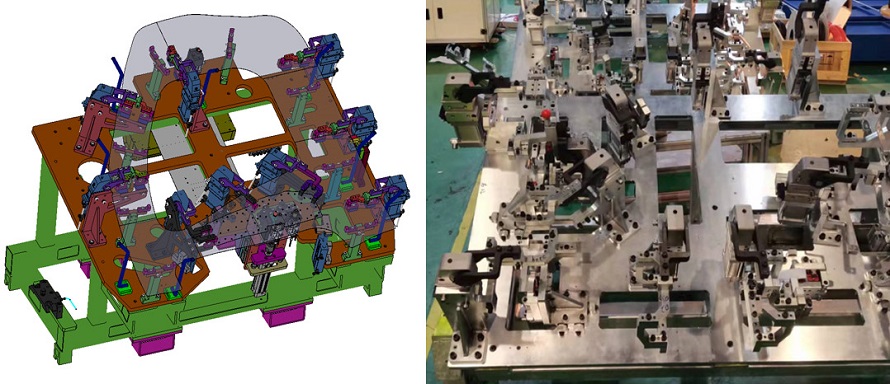
b.Inspection and verification: The diameter of the weld nugget in the post-weld inspection exceeds Ø6, and the welding cycle is controlled within the requirements.
c. Conclusion:
The material spot welding of integrally formed door knocker is relatively easy to realize due to the flat material and many welding spots, which is much less difficult than the automatic spot welding after forming, and the spot welding process adopted is also relatively traditional. The only difference is that the shape of the product is larger, which has certain requirements for the overall layout of the workstation; in the future, more and more integrated door knocker applications, the use of gantry-type automatic spot welding sheet will also be a good choice.
Tag: Introduction of Welding Process for Automatic Spot Welding Workstation for Automobile Door Knob Sheet-Suzhou Agera Automation Equipment Co.,Ltd.
Description: The fully automatic spot welding workstation for car door knockers is based on factors such as flat materials, many solder joints, and large and heavy door knockers. welding.
Key words: automatic spot welding workstation for automobile door ring blank, robot welding system for automobile door ring, welding process
Post time: Feb-16-2023